Problem Statement
Each life is an asset and we do not want an accident to ruin assets. While loading docks provide the means of a smooth flow of goods in industries like logistics, warehousing, distribution centers, manufacturing and shipping, the accident caused by truck reversal at loading docks & automatic doors may lead to loss of life or can cause serious damage to human life. The cause of accidents during truck reversal is mainly due to lack of perceptibility to the driver. The driver has very limited to almost no visibility of the truck’s background. It would be very exhausting to get another person to guide him/her during the reversal, there is a chance of human negligence too.

Common Practices
With an appropriate signaling system truck reversal accidents can be avoided.
- Commonly, through beam sensors are used to generate outputs which are processed through a PLC system, traffic lights are then used as a guide for drivers. This practice will only monitor the length of the beam that the sensor generates where it is installed and is not suitable for detecting only human presence. Besides, beam sensors can also have false triggering since there is no filtering of the signals.
- Like through beam sensors, light curtains can also be used but they also do not cover the complete detection area, since a light curtain is an array of beam sensors it is challenged to cover only vertical detection, and horizontal detection is missed. There is an additional cost of light curtain infrastructure, they are highly susceptible to damage or disturbance during the reversal process.
- Ultrasonic sensors are also used for this application, but ultrasonic sensors have very limited sensing range as well as accuracy and are affected greatly by environmental conditions such as temperature, humidity, and wind turbulence. As temperature increases, sound waves travel faster to and from the target, causing the sensor to calculate a shorter distance even if the target has not moved.
Solution
The purpose of the truck reversal application using BEA LZR®-Widescan is to provide a comprehensive solution to the problems stated above. The application consists of a sensor connected to the PLC which is processing the data collected from the sensor. PLC will trigger the traffic lights/ hooter to alert the driver.
The three outputs provided by the LZR®-Widescan are processed using a PLC algorithm, the traffic lights giving the driver an indication of the presence of humans in the safety field.
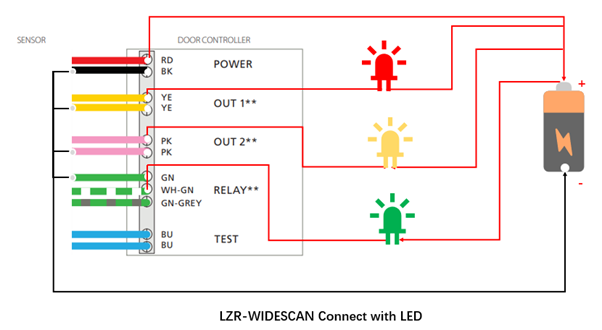
The truck reversal application can work with any type of automatic high-speed industrial door or loading dock with the mounting height ranging from 2mtr to 6mtr.
The LZR®-Widescan provides a state of art three-Dimensional Laser field which has three zones namely motion, presence, and safety. The 3D field consists of 7 curtains originating from the sensor. The depth of the 3D field is almost the same as the mounting height of the sensor.
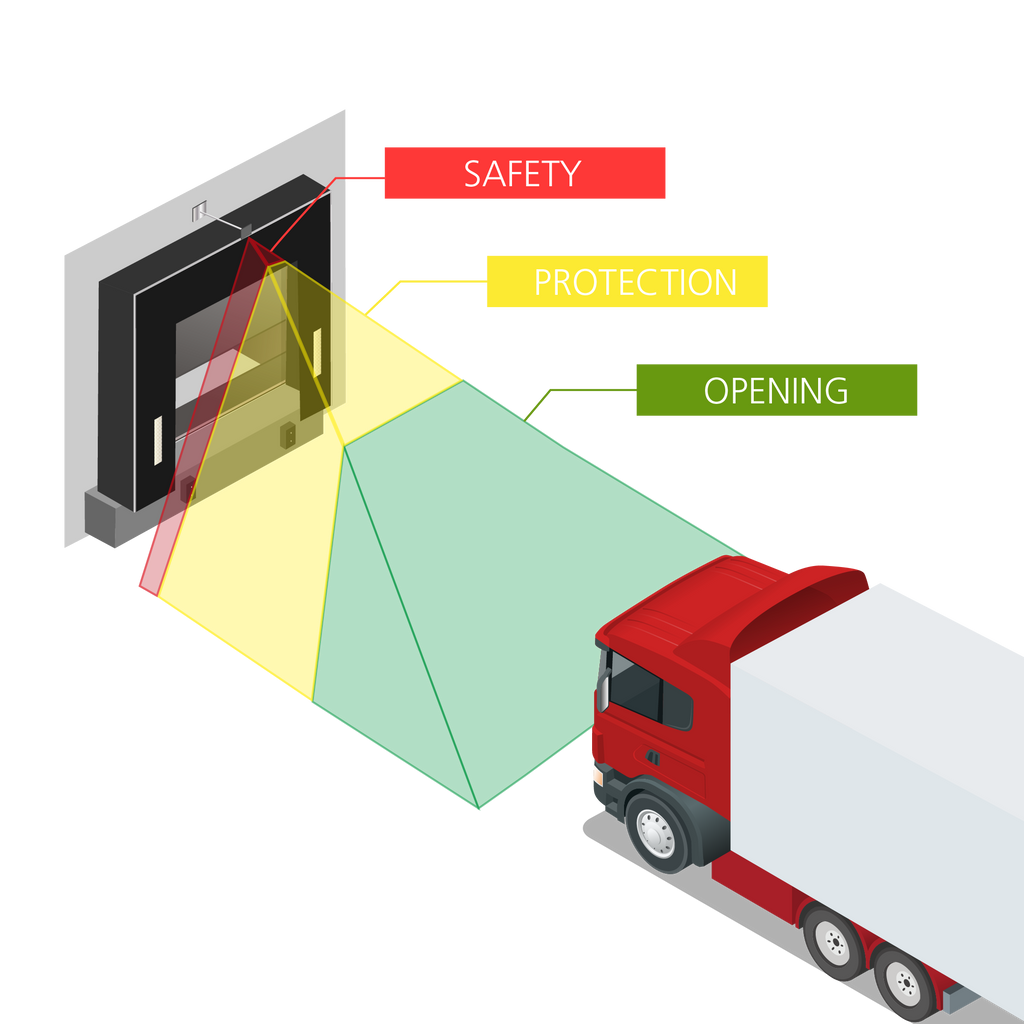
Field Pattern
The LZR®-Widescan has a diversified application range without being affected by environmental conditions. It is suitable for extreme temperatures ranging from -30 °C to +60 °C with IP65 compliance. The sensor does not require any additional infrastructure to set up.
Additionally, sensors can filter vehicles and humans.
In the case of only human movement, it allows users to half open the industrial door as well.
It can be configured to the requirements of sites using a mobile application or BEA universal remote.

At Actual Installation